Pick and pack errors
The process of picking and packing is a trivial task that can easily go wrong. With the demand for online grocery shopping on the rise, picking and packing errors can be irritating and affect a customer’s trust within a company and its employees. There is nothing worse than ordering an ingredient for a recipe and being left with an unusable item. Beyond the end-user experience, pick and pack errors can be traced to the back-end experience from grocery store staff. Errors and mistakes made while picking and packing reflect badly on the business, making the company seem unreliable driving shoppers away. At Mappedin, we have 6 tips on how to reduce picking and packing errors and create a stress-free shopping experience to improve your company.
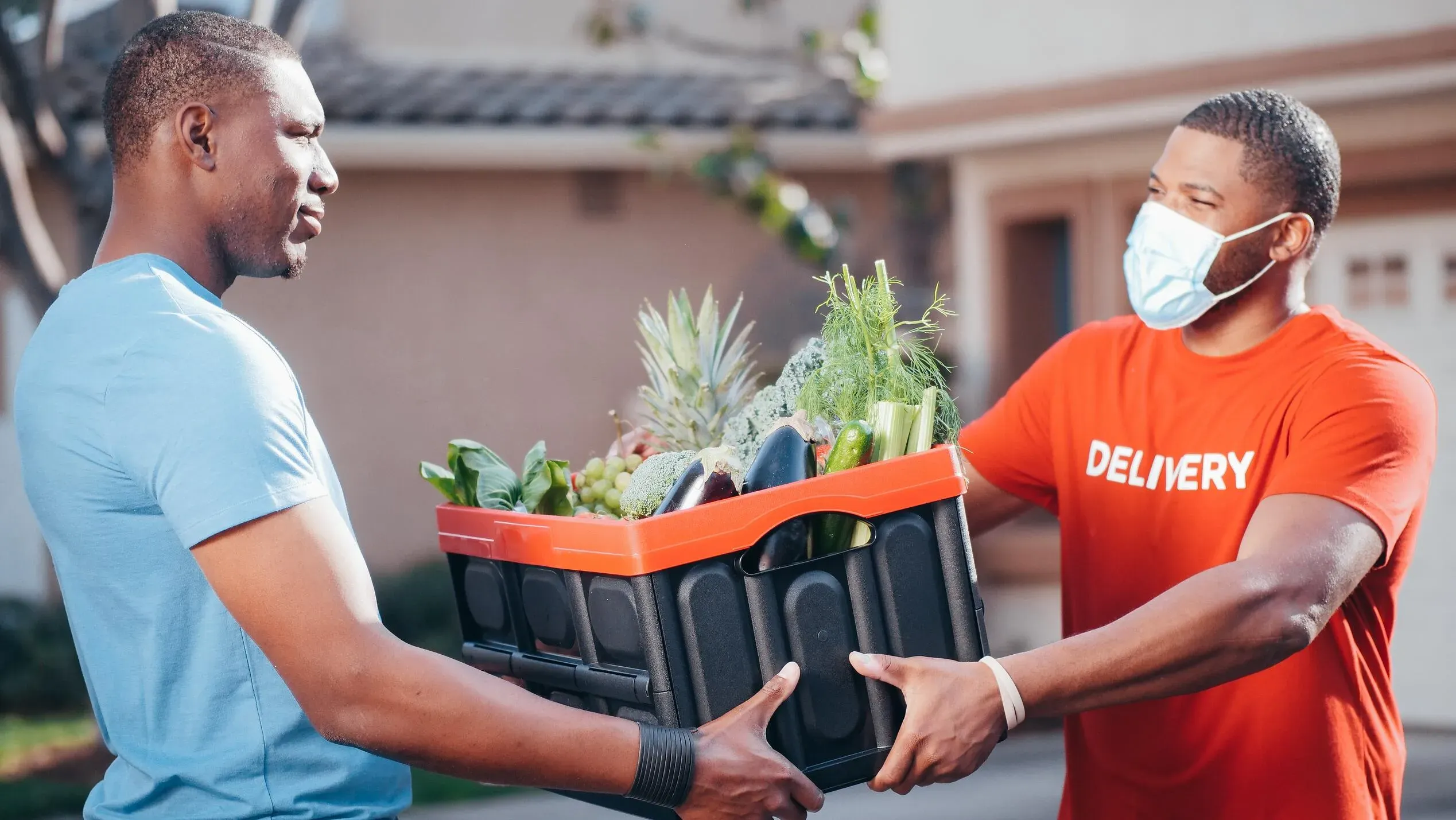
Indoor maps and wayfinding
Creating an optimal store layout for shoppers can be challenging and tedious when having to manually move a product’s placement over and over again to see what works best for picking and packing processes. Employees can utilize wayfinding systems to organize the spacing of grocery stores and make the most optimized pathing available to shoppers. This helps reduce picking and packing errors, as individuals can increase efficiency by swiftly navigating their way through a grocery store preparing orders accordingly.
Optimal pathing throughout the store
Pickers and packers can save time through navigation software that can route individuals to pick and pack in the most efficient direction based on their current location and the orders they need to fulfill. When managing multiple customers at the same time, the order picking process can be tricky to keep track of. Wayfinding technology allows individuals to create a shopping list upon entry so shoppers can plan their multi-stop route from the moment they enter the front doors and straight to the exit. Preplanning trips with navigation systems can be essential when looking to save time by avoiding inefficient wandering around a store.
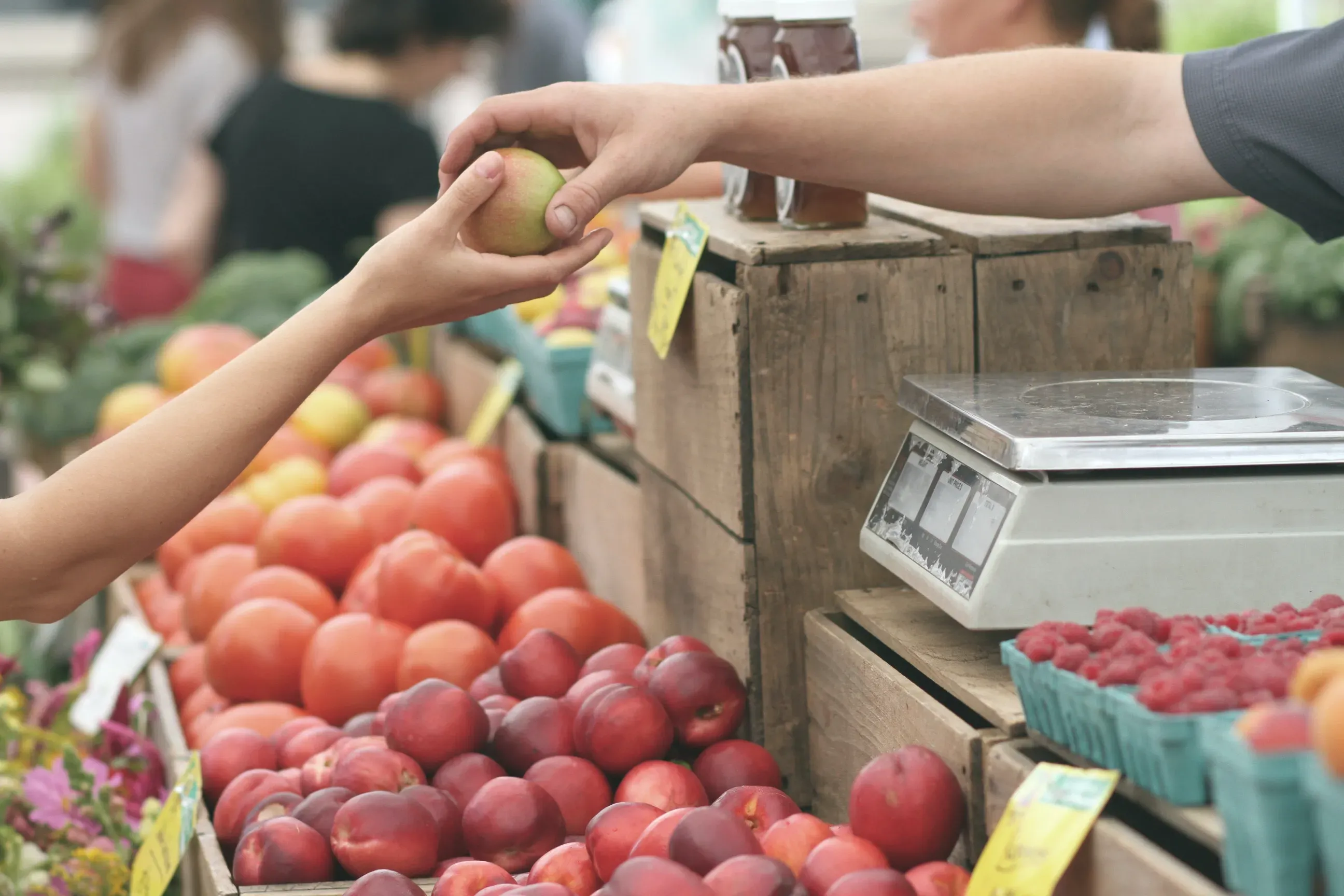
Map management and store layout planning
In-store workers are familiar with the entire space of the store as they travel through it every day, but employees who work in a corporate office may not be around as often. When entering the store they can be located to upstairs offices or any items they may need to check on within their store location. Company managers can also utilize wayfinding technology to collect data and see customers’ routes along with pick and pack trends. This allows corporate managers to reassess the spacing of their store location to see if a change is needed to optimize pathing routes. Corporate managers can use a Map Editor to make these changes and upload them in real-time, ensuring shoppers can navigate their way through the store with the most up-to-date information. A Map Editor guarantees that individuals can accurately navigate their way through the store and pick and pack items with ease.
Inventory management system
A management system can help a business keep track of their inventory and product data such as batch, SKU, brand, price, and more. Once an order is received and stocked on the shelf, it is essential that the items are in the right place to avoid pickers and packers picking the wrong items from the right locations. Grocery store workers can reduce the impact of incorrect orders by implementing an automated system that records the data of inventory and where items are placed. When moving items around the store, an automated inventory system can record the data. Stock clerks can scan orders when they are received and again when put away to reduce mistakes and ensure products are kept in the right locations and create an inventory list of where items are placed around the store. Giving workers technology to use in-store reduces tedious manual labour and creates a more efficient work environment. Pickers and packers can confidently reduce the number of wrong orders and increase productivity when they are sure the labels and prices of a product are accurate.
Planograms
Product visualizations
Searching for products can be time-consuming, aimlessly wandering through aisles in the store in search of a particular item. Planograms are visual representations of items displayed in a grocery store and they can be used to make the process of picking and packing easier when integrated into an automated inventory system. Pickers and packers can identify the items on the shelf before entering the store and visualize the products they need to reduce any error that could occur. Pickers can identify the locations of their desired items and skip aisles accordingly, saving time and energy when preparing a customer's order. Planograms can reduce time and money wasted through picking errors and increase workflow by ensuring the correct items are picked for each order.
Organized inventory
In a grocery store, there are a number of items to keep track of, and it is easy for items to get misplaced. Planograms can help operation managers keep inventory organized and improve workflow. When receiving an order, planograms can pick the optimal location for every item listed in their stock inventory, allowing operations managers to plan their floor plan to increase the efficiency of pick and pack methods. Planograms can also benefit new staff as they are learning the layout of the store. Managers can provide planograms during employee training to teach new staff where products locations are.
In-aisle scanning devices
Accurate order fulfillment
In-aisle scanners allow individuals to execute the pick and pack process as they go and reduce error rates. Using an in-aisle scanner while preparing orders can reduce picking errors by keeping all shopping information such as SKU and batch information in one digital place. A scanning device can help avoid the human error of picking the wrong item by validating that each item is picked correctly. For example, if a picker needed to fulfill an order with dog food, but accidentally added food for the wrong breed, an in-aisle scanner would notice and notify the picker that they made an order picking mistake. In-aisle scanning devices ensure shoppers get the exact products they ordered while being able to budget time and money. This helps avoid mistakes like giving a customer a useless item that they paid for and then straining business resources when they must process a refund. In-aisle scanners can account for customer preferences as well, for example, if a customer requested their avocados ripened, or if they prefer a certain brand of mayonnaise.
Analytics & insights
An analytics team can use the data from in-aisle scanning devices to see which products are being individuals are picking and in what exact order. For example, an analytics team could see that 90% of shoppers that are picking milk also pick eggs, showing that these two should be close to each other. An analytics team can track the route of shoppers and change the layout to make customers have the most productive trip to the grocery store.
Bagging placement technology
Bagging is a critical process of grocery shopping that often gets overlooked in helping to reduce picking errors. With multiple orders to keep track of, packing the order tends to fall off on the priority scale and mistakes may be made. Throwing items into a bag can result in the damaging of certain items. Grocery stores can implement technology that can order items in a bag at checkout to avoid errors. Technology can track which items are purchased and order them in the placement of the bag. This avoids the error of squishing bread if it is placed at the bottom or keeping all meats together to minimize money wasted from damaged items. This reduces the errors caused by inefficient packing and creates fulfillment in online shoppers when they receive their orders.
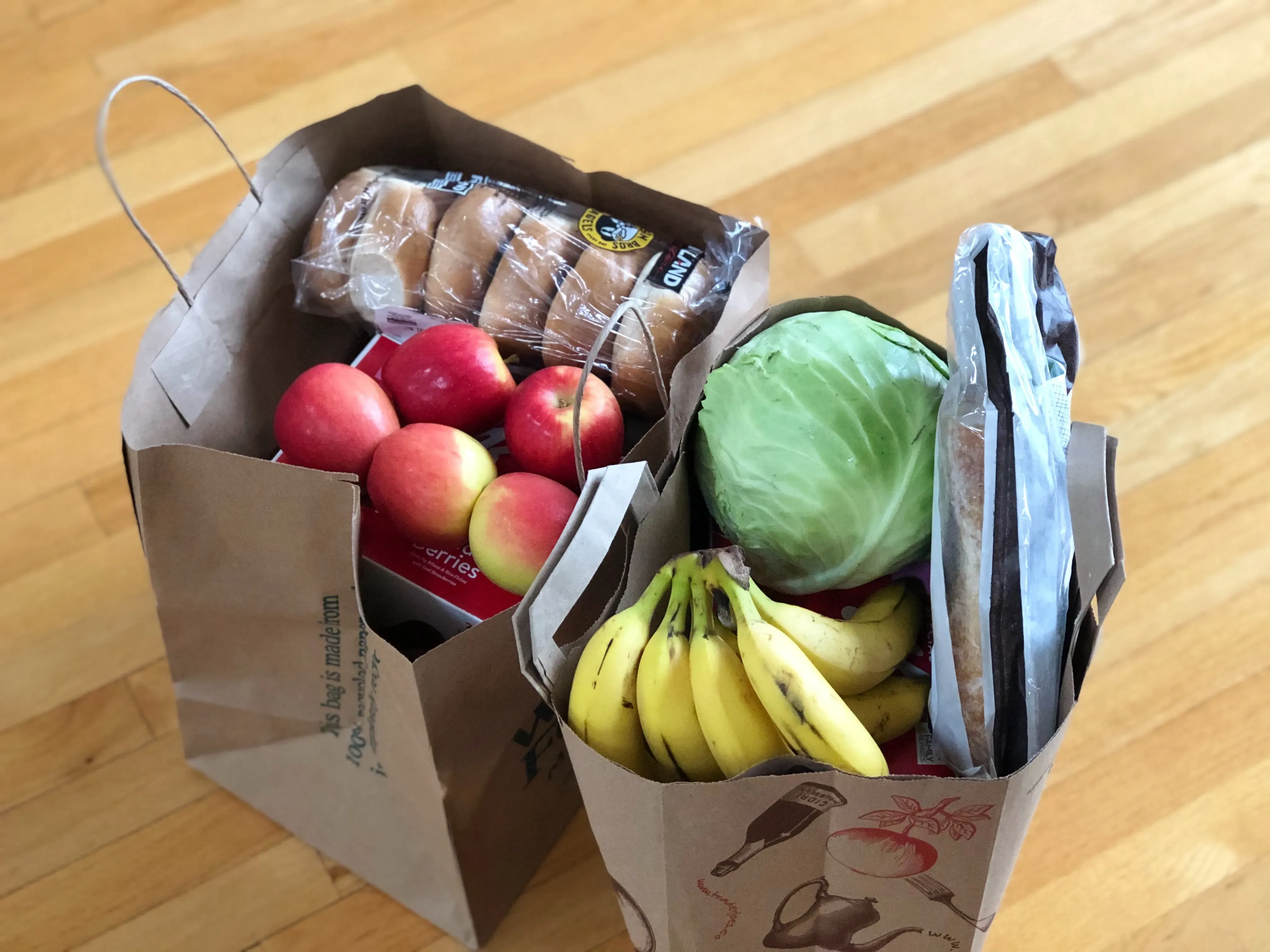
Mobile applications
When thinking about how to reduce picking and packing errors, a mobile application can be the solution. Mobile applications can combine all these tips into one by implementing a 3D wayfinding map, planograms, in-aisle devices, and bagging technology, all directly from your personal device and in one central easy-to-use application. Picking errors and mistakes can greatly affect the reputation of a business. That's why we recommend a mobile application to make picking easy and keep shoppers happy.
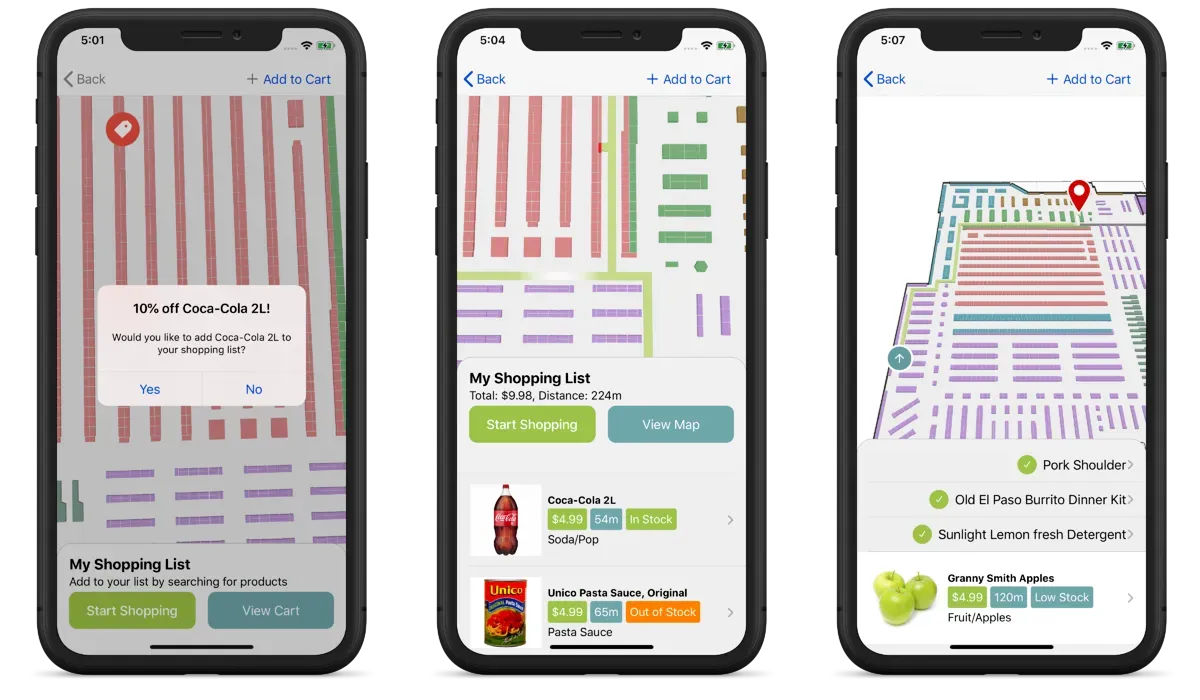
Reducing picking errors creates a stress-free shopping experience. Mappedin’s handy solutions can help shoppers save time and money by getting the ingredients they need while also promoting efficiency within grocery stores. To learn how to increase productivity and reduce human error by creating an efficient and optimized grocery store experience, visit our website or contact us today!
Tagged In
Share